Failure Tree Analysis
Failure Tree Analysis (FTA) is utilized in risk assessment and reliability engineering, specifically focusing on analyzing failures within a system. It commences with a particular undesired event, such as a system failure or undesired process, and then traces back through the system to identify the various potential causes or failures that could lead to that event. These causes are represented as branches of the tree, delineating logical relationships and dependencies between them.
On the other hand, Event Tree Analysis (ETA) involves the examination of potential outcomes resulting from different sequences of events. It commences with an initiating event and then explores the various possible branches of events that could ensue from it.
Failure Tree Analysis is a systematic and structured approach used to identify and analyze potential failures within a system. By mapping out the causes and effects of failures, FTA enables to proactively address risks and implement preventive measures to mitigate these risks.
Methodology of Failure Tree Analysis (FTA):
- Identification of Undesired Events: FTA begins by identifying the undesired events within the pharmaceutical production process. These events could include product contamination, equipment malfunction, deviation from process parameters, or any other failure that could compromise product quality or safety.
- Construction of the Failure Tree: Once the undesired events are identified, a hierarchical tree structure is constructed, illustrating the relationships between these events and their potential causes. The tree branches out to represent different failure modes, with each branch detailing the contributing factors or failure mechanisms.
- Analysis of Failure Causes: Through systematic analysis, each branch of the failure tree is examined to identify the root causes of failures. This involves brainstorming sessions, data collection, and expert input to uncover potential failure scenarios and their underlying causes.
- Assessment of Consequences: In parallel with identifying failure causes, FTA assesses the potential consequences associated with each failure scenario. This includes evaluating the impact on product quality, patient safety, regulatory compliance, and financial implications.
- Risk Prioritization and Mitigation: Based on the analysis of failure causes and consequences, risks are prioritized according to their severity and likelihood. Pharmaceutical companies then develop risk mitigation strategies to address high-priority failure modes, such as implementing process improvements, enhancing equipment maintenance protocols, or revising quality control procedures.
Failure Tree Analysis Example:
Consider a pharmaceutical company manufacturing sterile injectable drugs. One of the undesired events identified is microbial contamination of the final product. The failure tree is constructed with branches representing various failure modes contributing to microbial contamination:
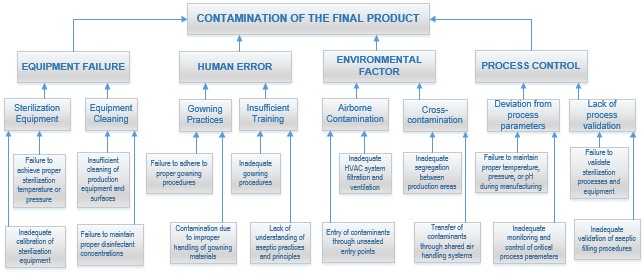
- Equipment Failure:
- Malfunction of sterilization equipment:
- Failure to achieve proper sterilization temperature or pressure
- Inadequate calibration of sterilization equipment
- Inadequate cleaning and sanitization procedures:
- Insufficient cleaning of production equipment and surfaces
- Failure to maintain proper disinfectant concentrations
- Human Error:
- Improper gowning practices:
- Failure to adhere to proper gowning procedures
- Contamination due to improper handling of gowning materials
- Insufficient training on aseptic techniques:
- Lack of understanding of aseptic practices and principles
- Inadequate gowning procedures
- Environmental Factors:
- Airborne microbial contamination:
- Inadequate HVAC system filtration and ventilation
- Entry of contaminants through unsealed entry points
- Cross-contamination from adjacent production areas:
- Transfer of contaminants through shared air handling systems
- Inadequate segregation between production areas
- Process Control:
- Deviation from validated process parameters:
- Failure to maintain proper temperature, pressure, or pH during manufacturing
- Inadequate monitoring and control of critical process parameters
- Lack of process validation:
- Failure to validate sterilization processes and equipment
- Inadequate validation of aseptic filling procedures
Each branch of the failure tree is systematically analyzed to identify
the root causes and assess the potential consequences of microbial
contamination. Risk mitigation measures may include enhancing
equipment maintenance schedules, implementing rigorous training
programs for personnel, conducting regular environmental monitoring,
ensuring strict adherence to validated processes, and implementing
robust quality control measures throughout the manufacturing process.